MDS and Rolls-Royce reach major milestone in the design & construction of the largest indoor aviation test facility in the world
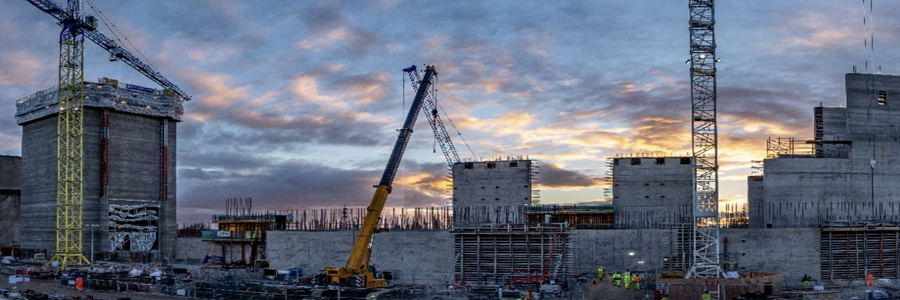
It has been just over a year since MDS was named prime contractor for the new Rolls-Royce facility in Derby and the building is already taking shape.
The facility takes the standard U-shape of indoor aviation test facilities, but the size, wall thickness, and additional features (such as X-Ray technology) that will be associated with the future engine testing arena are anything but standard. The gargantuan facility, located near Rolls-Royce’s head office and its hub for aviation engine testing, already dwarfs other test beds in the park. Currently sitting at 425.5-ft.-long with the main test bed cross section of 49 ft. by 49 ft., it will be the largest of any facility of its type. MDS has partnered with U.K. construction firm Buckingham Group Contracting Ltd. to erect the facility.
A major milestone was recently reached with the first of the twelve augmentor tube pieces being successfully installed. Fully assembled, the augmentor tube will be approximately half the wingspan of a Boeing 747-B. Each piece of the tube weighs in at 8 tonnes and needed to be escorted on large trucks through the narrow U.K. streets.
A critical part of any aviation test bed, the augmentor tube directs the engine exhaust gases and test bed bypass air to the back of the facility where it is diffused and released through a 123-ft.-tall exhaust stack. With engine mass flow rates continuously increasing as engine manufacturers strive to maximize thrust and efficiency, test facility design becomes far more complex and critical to the operational integrity of the facility.
Managing the immense amount of air flowing through and around the engine during a test is an important part of the design process since the airflow is a direct contributor to infrasound – low frequency noise that can have a detrimental effect on the integrity of the building as well as the employees working in close proximity.
MDS has a long history of designing state-of-the-art test facilities for Rolls-Royce and are at the forefront of research and technology in the narrow field of aeroacoustics, of which there are very few experts. Constructing the largest aviation test facility of its type in the world with an unprecedented amount of airflow poses a big challenge in this respect and our research and expertise in this area played a big factor in being named the prime contractor on this project.
Construction of the facility began last summer (2018) and seeing it come together with each pour of concrete has been an incredible journey thus far. It is an honour to be partners in the growth of Rolls-Royce as they embark on developing engines for the next generation of aircraft. The test bed will be capable of testing today’s engines as well as serve as a base for testing the new UltraFan®.